Aerospace company delivers seven times more aircraft
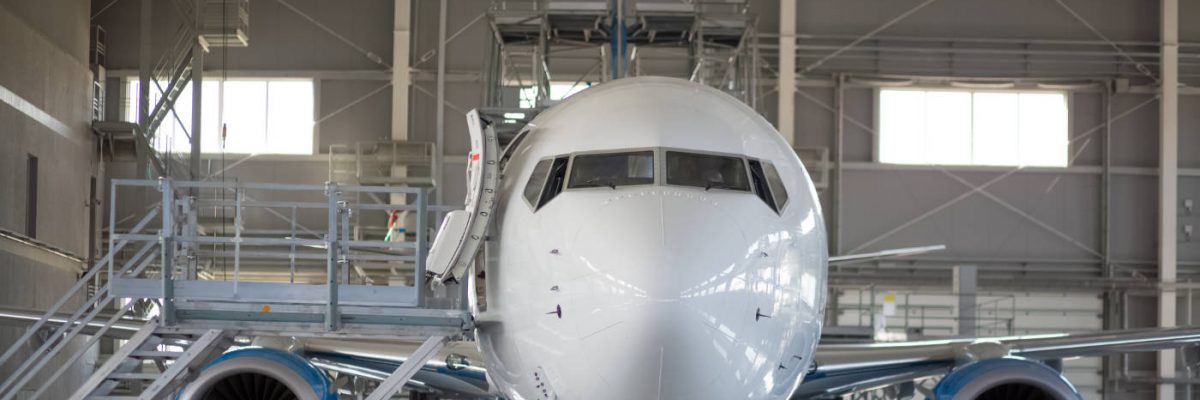
A start-up aerospace company focused on the design and manufacture of high performance and speciality purpose aircraft sought to improve on time delivery.
CornerStone Approach
CornerStone’s analytical professionals mapped the client’s entire workflow and manufacturing processes to identify key issues affecting its ability to complete and deliver aircraft on time. Issues addressed included: an inexperienced workforce; broken supply chain; and lack of business and shop floor processes. The team designed and implemented a plan to capture prioritised improvements as well as a structured management system to track and maintain performance.
Actions Taken
- Re-engineered the shop floor process and workflow to include work cells and kitting areas.
- Developed and implemented a system for managing production.
- Re-engineered the supply chain with the ability to identify and track long lead-team items.
- Designed and implemented a shop floor performance reporting system with the ability to track individual performances and to identify and resolve barriers.
- Developed and implemented a front-to-back Master Production Schedule.
- Developed production standards and dynamic productivity takt (the average time taken to move onto production of the next unit) reporting time.
Driver Goals
- Increase monthly aircraft deliveries to two within nine months and three within 12 months.
- Accelerate revenue streams through final delivery and progress payments.
Results
- Decreased engineering NMRs by 45%.
- Reduced wing takt time by 30 days.
- Produced a single Master Production Schedule.
- Increased aircraft deliveries to seven from just one in the previous year.