Paper company reduces unplanned engineering downtime by 60%
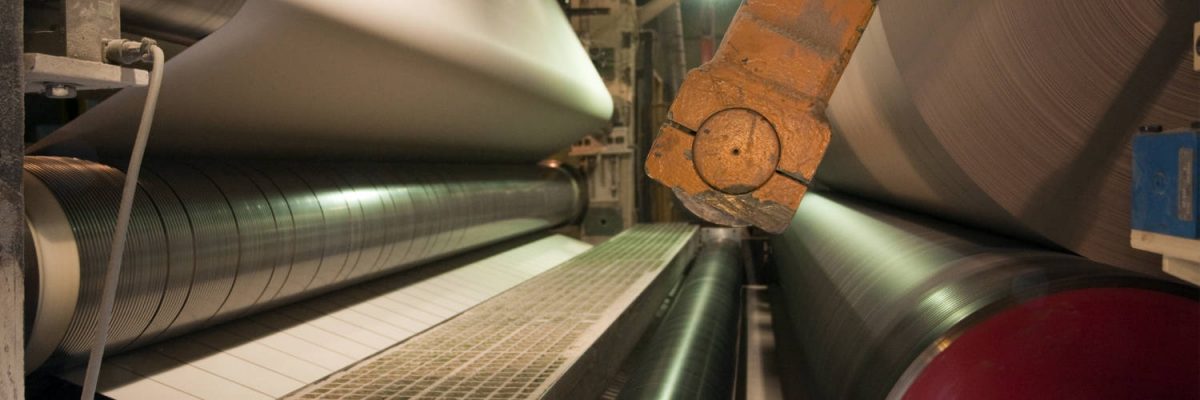
A world leader in papermaking was facing a significant amount of unplanned engineering downtime. This reduced the availability of all main assets, disrupted assets from realising their production targets, and ultimately caused significant delays and product waste.
CornerStone Approach
Cornerstone identified asset utilisation as the key driver to attack engineering maintenance. It then thoroughly analysed and mapped the client’s entire production workflow and engineering processes to pinpoint all key issues that negatively affected asset reliability. Subsequently, it analysed the maintenance routines and strategy, audited a number of maintenance shuts, involved all key personnel in the analysis of its findings and then developed a solution that focused on:
- Identifying “the right maintenance jobs” (and frequency)
- Developing a structured approach ‘to do the right jobs right, first time’.
CornerStone worked with us to capture cash quickly by implementing new processes which are ensuring sustainability of our improved cash position.Chief Financial Officer
Actions Taken
- Developed a maintenance strategy and maintenance routines.
- Designed and installed a system for planning all maintenance works and managing them on the shop floor.
- Developed and installed the maintenance planning tools, controls points, KPI’s and reports to allow for transparency, visibility & accountability.
- Developed and installed continuous improvement and knowledge management system to ensure that key learnings after each maintenance shut would result in improved performance.
Driver Goals
- Maximise asset utilisation
- Reduce unplanned engineering downtime
- Increase works completion rate while maintaining strict safety and keeping the costs under control
Results
The unplanned engineering downtime has been slashed – and sustained – by almost 70% on the bigger assets, and by 10% to 15% on smaller assets.
- Works completion rate increased from 60% to 95% while maintaining safety levels.
- Maintenance routines and work completion on-time provided improved reliability, smoother start-ups and thus increased machine availability and reduced overall product waste.
- Improved knowledge management and staff morale.